In this episode of the Dust Safety Science Podcast, we are speaking with Ali Alnajdawi, fire investigator at Forensic Laboratory Department and electrical engineer with the Ministry of the interior of Jordan, about the large grain silo explosion that occurred at Port Aqaba in 2018.
At the time of recording, we are analyzing the data for our year-end incident report, and this explosion appears to be the most devastating confirmed dust explosion in 2018. The Port Aqaba incident took the lives of seven workers and injured several more. Ali was involved in the subsequent investigation and in this interview we discuss:
- The causes leading up to this incident?
- Where did ignition occur and how did that propagate throughout the facility?
- What processes are being put into place to avoid this type of incident in the future
An Overview of the Port Aqaba Grain Silo Explosion
On May 14, 2018, old silos at a grain storage terminal were being emptied and dismantled at Port Aqaba, Jordan. The terminal had 75 silos, each one forty-five meters high and nine meters in diameter. Each silo could hold 200,000 tons of wheat.
Next to the silos was a fifty-five-meter tall tower that contained a grain conveying system including bucket elevators. The bucket elevators and conveying system ran down to underground tunnels containing a horizontal conveying system and relevant structures and machinery for transporting the wheat from the silos into the road trucks.
The property owners, Aqaba Development Corporation, had emptied the silos and transported most of the wheat to a new location. The dust suction systems were also dismantled, the electricity cut off, and the Abu Ghraib company was commissioned to demolish the silos using one ton of dynamite and time delay capsules.
This subcontractor had received a risk assessment report alerting them to the risk of the dust explosion and the need to clean the silos before work commenced. According to Ali’s investigation, they did not comply and a dust explosion occurred during the decommissioning, killing seven Jordanian workers in total.
Below are some site photos that Ali has supplied showing the destruction caused by the series of explosions.
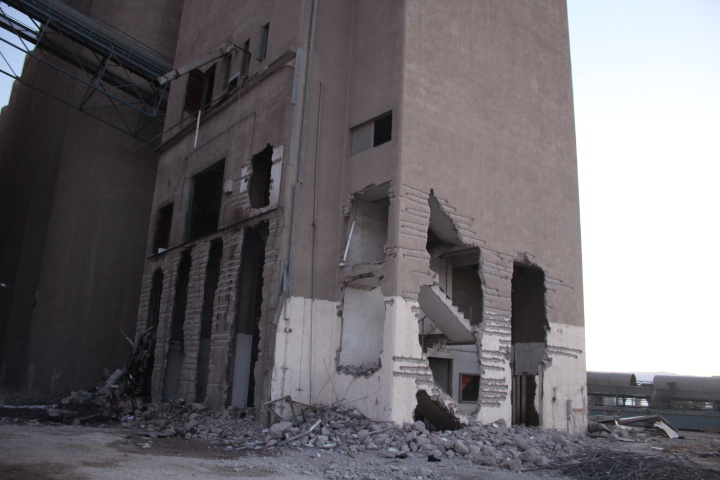
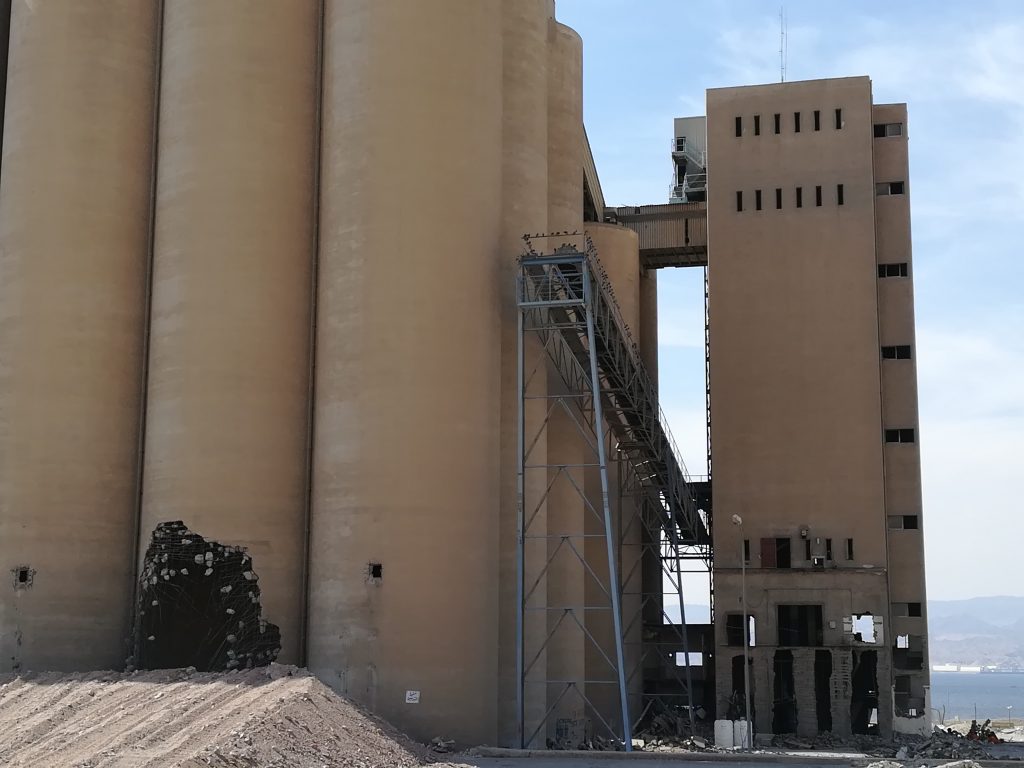
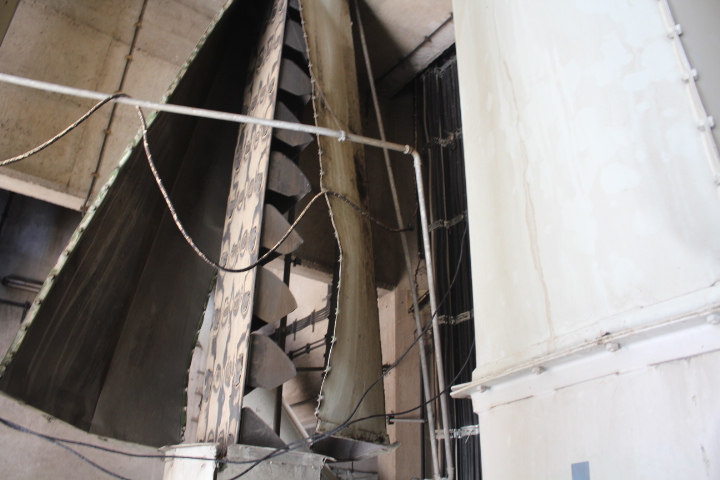
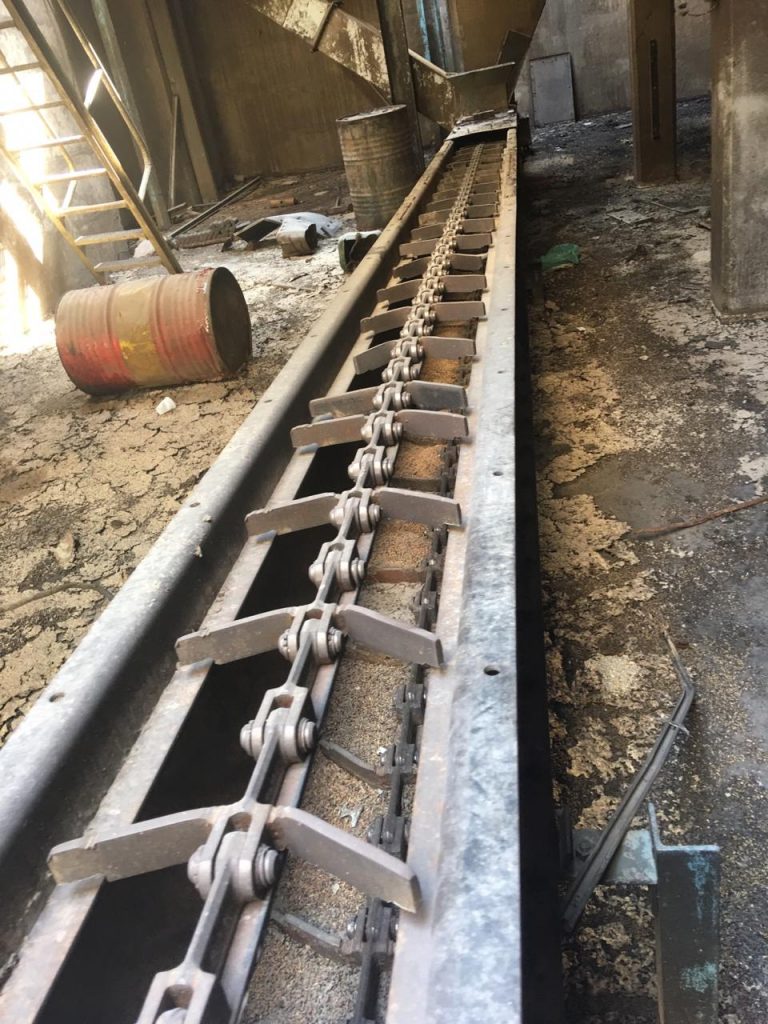
After an investigation, Ali Alnajdawi and his team concluded that the five main elements required for a dust explosion were present on the third floor of the tower, and in the grain conveying system:
- Dust (in this instance, wheat)
- A confined space (the conveyor system)
- Dispersion of the dust by workers or a primary explosion
- Oxygen in the air
- An appropriate ignition source
The ignition source was not determined, but Ali believed that it was a spark from iron being cut to place the dynamite. It triggered a combustible fire that quickly turned into a primary dust explosion. Then it spread into the underground tunnels, causing secondary explosions due to dust deflagration.
Lessons Learned From the Port Aqaba Incident
Ali said that two lessons were learned from this incident. The first involved the two serious mistakes made during this incident:
- The company dismantled the dust suction system and cut the electricity left wheat inside the silos, conveyors, pipes, and underground tunnels.
- The same contractor did not heed the warnings and went to work without cleaning the silos and removing the dust.
The second lesson addressed the safety procedures that should be used to prevent another combustible fire or dust explosion. Ali couldn’t locate any precedent for such cases in Jordan, so he referred to OSHA and NFPA codes such as well as the European standards related to dust safety to develop an action plan for future hazards at Port Aqaba.
Ali started by dividing the incident site into three zones according to hazard:
- Zone A (most dangerous): the tower and underground tunnels with all the confined spaces
- Zone B: the main silo columns, which were enclosed with small venting holes at the top and sides
- Zone C: The main silo columns with small venting holes at the top and sides but were partially demolished and nearly ready for demolition.
Each zone had different safety procedures and work steps to eliminate all the dust explosion risks, such as:
- Ventilation
- Vacuuming
- Housekeeping
- Dust washdown
- Ignition source control
The plan included:
- Specific explosion filter vacuums that were compatible with NFPA 70
- Using a water-spraying machine for dust washdown compatible with OSHA and NFPA 70
- Installing explosion-proof lights in dark places
Ali successfully implemented his plan and worked with a dedicated team to eliminate all combustible dust hazards at the site. You can read his report of the Port Aqaba incident here.
Ali’s Recommendations
Based on his investigation of the Port Aqaba incident, Ali recommended the implementation of a proper management system to minimize dust fire or explosion incidents. This could be accomplished by:
- Establishing an allowable official value for dust accumulation;
- Ensuring that the proper equipment is available for routine cleaning;
- Inspecting the areas where combustible dust could accumulate;
- Determining
frequency of cleaning; - Keeping dust suction system active during decommissioning and cleaning;
- Ensuring that personnel are trained on appropriate cleaning
techniques ; and - Preparing an awareness program to increase worker awareness of combustible dust hazards.
Ali compared a worker employed in a dusty place to an explosives expert who is trying to stop a time bomb: if he hits the wire, it would cause the bomb to explode. As he states many personnel who work in dust handling facilities have no awareness in this area, and that needs to change.
Conclusion
We were truly honored to interview Ali and hear his perspective on this tragic 2018 incident in addition to the lessons that he and his team learned. These insights from around the world bring us closer to our goal of developing systems and processes to avoid the combustible dust fires and explosions that so often end in tragedy. It is our hope that the lessons learned from this incident can be used to develop better approaches to grain silo explosion prevention and decommissioning of powder and dust handling facilities.
If you would like to discuss further leave your thoughts in the comments section below or you can reach out to Ali Alnajdawi directly:
Email: [email protected]
LinkedIn: Profile
Resources Mentioned
Dust Safety Science
Companies
Aqaba Development Corporation
Organizations
Standards
Incidents
Thanks for Listening!
To share your thoughts:
- Leave a note in the comment section below
- Ask a question to be answered on the show
- Share this episode on LinkedIn, Twitter or Facebook
To help out the show:
- Subscribe to the podcast on iTunes
- Leave a review and rate our show in iTunes to help the podcast reach more people
Download the Episode
Full Episode Transcript
Chris: [00:09] Welcome to episode number 13 of the Dust Safety Science Podcast. We’re looking at creating a global community focused on workplace safety and industries handling combustible dust and powdered materials. In today’s episode, we’re doing an interview with Al-nadawi out of Jordan. And Ali is a forensic laboratory department investigator, fire investigator and electrical engineer with the Ministry of the Interior of Jordan. And what we’ll be covering today is, is a very large silo, grain silo explosion that they had there in 2018. So this was actually at the time of recording. We’re just analyzing the data for our year end incident report. And this explosion unfortunately, was the most devastating confirmed dust explosion that we have in 2018. So it took the lives of seven workers, five on the day that happened and then two on subsequent days and injured a number more. And what’s interesting, that’s actually a couple of things that are interesting about this specific incident. Even though it’s tragic, it actually happened during decommissioning of the silos. So they’re moving it from Port Aqaba in Jordan to another location. And they had started emptying out the silos, and they were going to demo the building. And then the subcontractor didn’t complete the cleanup. And that led to a primary explosion and, and secondary explosions, which then caused the devastation.
Chris: [01:35] The reason to get Leon to talk about this, he reached out to me and explained the process, showed me some pictures of this really tragic and devastating incident, and he and his team really dug in to say, why did this happen? And how can we stop it from happening in the future? And in this interview, he really shares a lot of great insights how he went and looked at OSHA regulations, how he went and looked at NFPA brought all that material together to come up with a process for decommissioning silos in the future and a process that they can apply for their grain handling facilities throughout Jordan. So in this material, we’ll definitely include it in the interview here. And we’ll try to include some of the material that he’s created in the show. Notes that dust safety Science.com slash 13 for this episode. And I just want to say that it was really an honor to have Ali on. And I know this is a really tragic and sensitive incident, but the lessons learned that he pulled out of it and the material that he’s helping to share are really something that’s going to help decrease the incidence of this happening in the future.
Chris: [02:30] So I want to say thank you, as always, for listening to the Dust Safety Science Podcast. I want to encourage you to check out the show notes and to listen through to the end of the episode, as I think there’s some really great material and I really look forward to hopefully as we build out this community, build out our awareness and education, that we can reduce the chance of these kind of incidents happening again in the future. So thank you again and I hope you enjoy today’s episode with Ali. Welcome to the Dust Safety Science podcast. In today’s interview, we are having a discussion with Captain Ali Alnajdawi from the Forensics Laboratory Department in the Ministry of the Interior in Jordan. About a grain silo explosion that they had this year. This was actually one of the most devastating explosions that we recorded in 2018. That was actually confirmed dust explosion. And I wanted to have Ali on to really talk through what they’ve found in their investigation. I think there’s a lot of interesting lessons learned that we can pull out from this really tragic incident. So, Ali, I want to thank you for coming on the show today.
Ali Alnajdawi: [03:31] Thank you, Dr. Chris, thank you so much.
Chris: [03:34] Thank you. And I and you don’t have to refer to me as Dr. Chris throughout the interview, but I appreciate it, but Chris works as well. Okay, so earlier in the year, when we were coming up with our mid-year incident report in the middle of 2018, Ali actually emailed me about this, this explosion that they had in Port Aqaba, Jordan. So Port Aqaba is just off the Red sea, which is separating the Middle East and Africa. And we kind of go up there. There’s some tributaries that go into the port. And there they had this grain silo that they’re actually moving. So they started taking material out of the silo and they were going to, to demo it. And unfortunately, they had a pretty large scale dust explosion there that resulted in multiple fatalities. And Ali was nice enough to reach out and just say, I know you guys are doing this type of research. As we come up with information, I’d like to share it. So we share that in the incident report. And now he’s here today to go through their findings from looking into that incident. So Ali, I want to thank you again. And maybe as a starting point, can you briefly describe your role with the forensics laboratory department in the Ministry of the Interior in Jordan?
Ali: [04:45] Okay. I have been working at the forensic laboratory department in Jordan since 2007. The forensic laboratory Laboratory department in Jordan has qualified technicians and contains most recent analysis equipment. It is accredited by ISO 1702 five and did several twinning projects with different countries around the world. The last one was with Airline forensic laboratories. I started in the fire investigation section and now I am the head of the section. I am an electrical engineer with a demonstrated history of working in fire investigation, electrical fires, vehicle fires and fire protection assessment. I am also a combustible dust investigator. I attended many courses and workshops inside and outside Jordan about combustible dust hazards. Assessing dust parameters, dust control and process safety management. Also, I am an arson and gunshot residue analysis expert using a scanning electron microscope.
Chris: [05:55] Thank you for the background, Ali. That helps. And as the listeners that have been listening to a few episodes now from this year, we’ll know our focus for 2019 is understanding Combustible dust as a global challenge and developing global solutions. So to hear your background and how you know how far away you are from at least where we’re recording here in Nova Scotia, in Canada, I think that really fits along the line. So I appreciate you taking the time in terms of the port by incident. Can you describe the terminal layout? So this was a grain storage terminal. And can you describe what that looked like and maybe go into what happened that day?
Ali: [06:33] Sure. Aqaba terminal contains 75 silos, each with a diameter of nine meters and a height of 45m, and were used to store 200,000 tons of wheat. Next to the silos, there is a tower with 55m height, which contains a grain conveying system and relevant piping. All the conveyors and piping are attached with ducting columns down to the underground tunnels. The underground tunnels consist of three multi-level corridors containing the conveying system and relevant structures and machinery for discharging the wheat from silos into road trucks. The tunnel length is. Is 150m approximately. Now about the details of the incident. The incident happened on May 14th, 2018. I mean, about eight months ago now, two months before the incident, the silos company had evacuated the silos and transported the majority of the wheat amount to the new silos in the new seaport, where the old port was sold to set up tourist resorts. Also, the Silos Company dismantled dust suction systems and cut off electricity. The main contractor for the removal of the old board was submitted to the Arab International Company for Construction and Contracting, which commissioned a subcontractor, Abu Ghraib Company, to demolish the silos. Abu Ghraib Company signed an agreement with a Turkish company. It’s called igniter, to demolish silos using one ton of dynamite and time delay capsules. The Turkish company carried out studies to demolish parts of the silos and made holes and iron cutting in main construction columns to place the dynamite inside it.
Ali: [08:47] Aqaba Development Company, which is the owner of the old board, has warned through the risk assessment report submitted to the subcontractor Abu Ghraib Company, for several dangers, including the risk of dust explosion and the need to clean the silos before starting work. But the subcontractor did not comply with these warnings and did the work without cleaning the silos and removing the hazards. In the first week of the work, a dust explosion occurred and killed seven Jordanian workers. Five of them died on the same day and two in the following days. After the detection from me and my team, we concluded that the dust explosion occurred on the third floor of the tower in one of the grain conveyors. As a result of the availability of the five main dust explosion elements, which are the wheat dust, the confined space which is the conveyor, the dispersion of the wheat dust, and the availability of oxygen, an appropriate ignition source. Actually, it was unknown the ignition source, but the probability that it was from the iron cutting because of the hot work there was an iron cutting dust explosion that started as a combustible fire, which quickly turned into a primary dust explosion. Then it spread into the underground tunnels, causing secondary dust explosions as a result of dust. Deflagration.
Chris: [10:41] Wow, that’s quite a thorough investigation to pull that information out. And I think I just want to highlight a couple things. We’re going to go into the lessons learned that Ali and his team learned. But I just want to mention a couple things on the broader scope. This this was actually decommissioning of a silo. So I’ve seen in the last two years of the instant database, a number of cases where abandoned silos have caught fire. Sometimes it’s due to vandalism, sometimes it’s groups of kids or people are inside them. And if those aren’t cleaned up and decommission properly, I could see this kind of issue arising. So it’s it’s good to get that message out there. And then even if you are actually moving it or tearing it down, quote unquote, properly like we saw here, there are cautions that need to be to be thought of. And in this case, the the lead contractor had a risk assessment that that showed that. But then the information wasn’t really transferred down to the subcontractors. So I want to ask you what kind of lessons you pull through with the forensics laboratory department from this explosion incident?
Ali: [11:49] Actually, we learned two lessons from this incident. The first lesson is that there were two mistakes that were made, and they caused the incident. The first mistake was done by the silos company when they dismantled dust suction systems and cut off electricity. And they kept a small amount of wheat inside the conveyors and pipes and underground tunnels and inside the silos. That action created the existence of four of the dust explosion elements: the wheat dust, the confined spaces which contain the conveyors, the pipes and the ground tunnels. And the third one is the dispersion of the wheat dust and oxygen. So at that time the place was ready and waiting for an appropriate ignition source. Actually, it was so easy in that time to prevent any hazard and made housekeeping if the silos company kept the conveying and suction systems working until they cleaned the place and transported all the amount of the wheat before an evacuation. The second mistake was made by the subcontractor, Abu Ghraib, when they did not comply with any warnings and did the work without cleaning the silos and removing the dangerous dangers and hazards without the supervision of safety engineers. That action caused the president to use the fifth element, which is the appropriate ignition source of the Pentagon dust explosion at the Pentagon. So now when the incident happened, I and my team detected the site of the silos of the tower. We found that the dust explosion happened in one conveyor and extended to cause a secondary dust explosion in the attached underground tunnels, but the place contains many conveyors and pipes and was attached with other underground tunnels, and some of these places were awaiting ignition to explode.
Ali: [14:11] So this leads us to the second lesson from this incident. The second lesson is what are the safety procedures we should use to prevent the occurrence of any combustible fire or dust explosion before starting the work again. Indeed. I didn’t find any previous experience about dealing with such a case. I consider this case as unique, but I refer to OSHA regulations and NFPA codes like NFPA 61, 6869, NFPA 70, and NFPA 654, also for European standards related to dust safety. I divided this site into three zones according to the hazard zone A which is the most dangerous zone. It is the tower and the underground tunnels where all the confined spaces, I mean the conveying systems and the relevant piping are located. Zone B, which is the main enclosed silos. Columns provided with the small venting holes at top and size. Zone C, which is the main enclosed silos column provided with small venting holes at top and side, but has been subjected to a partial demolition earlier and nearly ready for demolition. Each zone has different safety procedures and work steps. The tunnel floors were covered with a thick layer of a mixed organic origin. Compound components are mostly formulated from wheat seeds, seed dusts, rat rats, feces. Promulgation residues. Dry and wet muddy compound I mean sludge on the top of the ducting structure.
Ali: [16:08] Still still having a good batch of accumulated quantities of wheat. The place has a bad odor. Areas exist, especially at areas where the wet sludge exists. Harmful steel structure intrudes, infringes steeps, slopes and in unleveled corridors are found all over the tunnels and ducting spaces. Darkness and like lack of good lighting, which may perform a danger issue on laborers doing the cleaning job. Ducting and piping structures are covered and have a considerable quantity of dust. The main idea of my plan is to eliminate all the dust explosion elements by ventilation, vacuuming, housekeeping, dust, washdown, and ignition source control through many parameters like minimum ignition temperature of the wheat, deciding, measuring the humidity, the low explosion limit, minimum ignition energy, minimum explosion concentrations, dust particle size and accumulated dust layer thickness. And also my plan, taking into consideration the combustible dust, personal protective equipment, oxygen safe limit for personal entrance. We also used specific explosion filtered vacuums for hazard locations compatible with NFPA 70. I mean, for example, it should be non spark, fully grounded with a specific motor speed noise, vacuuming pressure, etc. using a water spray machine for dust Washdown compatible with OSHA and NFPA 70. Housekeeping according to OSHA regulations. Explosion-proof lights and dark places. Actually, I have implemented my plan and have been successful through a dedicated team that I have trained and have already eliminated all the hazards in the sites.
Chris: [18:31] Wow. Thank you for sharing those lessons learned and that kind of detailed view of reviewing this incident and then some of the things that are needed to to reduce the chance of happening in the future and then what you’re actually putting in place. I’ll share with the listeners this will be the Dust Safe Science podcast episode number 13. So if you go to dustsafetyscience.com/13, we’ll include links to the incident report description of the port Aqaba incident. Maybe some images that I know Alice provided. And if they get their final report released and put out and that’s allowed to be public as well. We’ll try to share some of that information so you can come back to the website and get access to that material and see the process that he’s put in place. And from my understanding there, either the site has now been demolished or they’re in the process of demolishing it. Is that right, Ali?
Ali: [19:22] Yes. It’s already demolished. Yeah.
Chris: [19:25] Okay. I think it was actually earlier this, this week of recording maybe.
Ali: [19:29] Yes.
Chris: [19:30] Which is, which is great to see. They were able to go in and prove those changes. And at the end of the day do it right. But it’s really tragic to know that we had to actually have those lives lost. First, I want to sort of take a step back from your experience on a higher level and just ask if there is already any history of combustible dust incidents within Jordan or that you know of in that area.
Ali: [19:54] Jordan contains many facilities and companies deal with dust. And through my experience as a fire and combustible dust investigator and through a general overview of dust fire incidents in my country. Jordan. Approximately 1 to 2 incidents happen yearly. The majority of these incidents were. Combustible fires. I found that less than 20% of these incidents were caused by dust explosions. For example, through 11 years of my work in this field since 2007, up to now in many test fires, incidents occurred in Jordan. Most of them have been in grain mills, but just four of them caused a dust explosion. Two of the dust explosions happened in Jordan. Happened on the same grain mill in the same year in 2013. While the third one happened on the grain silos in Ramtha City in 2011. This incident caused minor injuries among workers and minor damage in the facility, while the latest one, which is the Aqaba Silos dust explosion, caused seven deaths and huge damage inside the silos. Actually, in recent years with the increase in dust fire incidents, the Crisis Directorate in Jordan has activated the emergency plans and increased the awareness of the facilities that produce dust or dealing with dust from the risk of dust, explosions or combustible fire. But the problem that still exists is the actual application of these plans from the facilities.
Chris: [21:58] Thank you again for compiling that information and sharing. I think it helps. We’re doing it a lot with the instant database in North America, and we get some coverage in other countries, but not nearly enough and not a very big proportion of what’s actually happening. So to have you come out and share what’s going on in Jordan and in your country is really of immense, immense value to what we’re doing. You mentioned a lot of the history, a lot of what you learned from this incident. Are there any changes that I know you guys are being very proactive on this, which is really good. Are there any changes that are being put in place to prevent future incidents today?
Ali: [22:36] Oh, yes. Actually, I believe that a proper management system needs to be put in place to minimize dust, fire, or explosion incidents and maximize effective housekeeping plans. This could be accomplished by establishing an allowable threshold value for dust accumulation. Ensure proper equipment is available for cleaning. Routinely inspect the identified areas where combustible dust could accumulate. Also determine frequency of cleaning and ensure that personnel are trained on appropriate cleaning techniques. Preparing awareness programs with scheduled timelines, for example daily, weekly, periodically to raise combustible dust hazards understanding between workers and also, for example, doing practical experiments that simulate dust hazards and taking lessons from previous incidents. I think that the organization should come up with the idea that the worker who works in a dusty place is like an explosives expert who is trying to disrupt the atom bomb. If he hit a wire, it would cause the bomb to explode. I believe that fear reduces recklessness and mistakes. One of the most important things I want to focus on to prevent such future incidents is the evacuation of all the facilities that were dealing or producing dust before the evacuation, and leaving the facility abandoned. The company must, or the facility must, do full housekeeping inside the facility and make sure it is free from any hazards. And taking into consideration that the personnel who will work in the evacuated facility after them have no awareness in this area.
Chris: [24:51] Thank you for sharing that. That analogy of workers that are working in a dusty environment are really, really working in a time bomb. And I think that’s true in a sense, in that if you have all four of the five sides of the Pentagon present, then you’re really just missing that ignition or tripping that wire. And that’s an interesting way to think about it. And I think if we had more training in place and more awareness, that would really help. I think that’s all we really can cover for today. But I really do appreciate you going through this incident because like I said at the outset, it’s a little bit different outside the scope of what people are thinking about in terms of their normal thinking of, okay, I’m running this plant, running this factory, this facility and the processing operations. Every day there’s these hazards. Then it’s really a full scope way of thinking, well, okay, how do we get a startup going? How do we do decommissioning? And as this instance shows, these can cause real world injuries and fatalities and are really important to consider. And I’m also really happy to see the really proactive stance that you’re taking with your work, helping getting out there. And I appreciate you reaching out to us and I appreciate you sharing your story.
Ali: [26:00] Thank you, Chris, thank you for your time today. Really, I appreciate sharing my information with the community. Thank you very much.
Chris: [26:10] Thank you. Ali. And I just wanted to give you one last chance. Is there anything else you’d like to kind of leave the listeners with from your experience here?
Ali: [26:18] No, but just, I do encourage them to follow your website, Dust Safety Science because it’s very useful and has a lot of information inside. And I hope that everyone has any new information about the dust fire, dust explosion to share with this website.
Chris: [26:45] Well, thank you. I really appreciate that, Ali. And, thank you again. And hopefully we can have you on the podcast at a later time, but not under these same circumstances where it’s after something’s happened. But to celebrate the success of these new programs you’re putting in place.
Ali: [27:01] Thank you very much.
Chris: [27:02] Thank you. You have a great day.
Ali: [27:03] Yeah. You too. Thank you.
Chris: [27:05] Wow. What an interview with Ali Nachtwey. And I really appreciate him coming on and sharing what he and his team have learned from this really tragic incident in 2018. It’s really, really terrible to see this happen. But the tact and the approach that they’re doing where they’re analyzing it, trying to pull in the best information from around the world to develop systems and processes to avoid in the future is really inspiring to see. And I was really honored to have Ali on and discuss this with his team. So in the show notes at dustsafetyscience.com/13. We’ll have transcripts of this episode or description of what we put up. We’ll also try to include links to Ali so you can contact him about the material he’s creating. And just so you can learn from this incident, that’s really, I think what I was talking to him afterwards. What he wants to get out of this is he wants people to learn from this tragic incident and also to stop it from happening in the future. So I hope, at least with this interview and this podcast, we can play a little part in helping with that. So as always, I want to thank you for listening to the podcast and I’m looking forward to moving through it 2019 as we continue to learn Combustible Dust as a global challenge. And pulling this information to avoid these kinds of incidents from happening in the future.