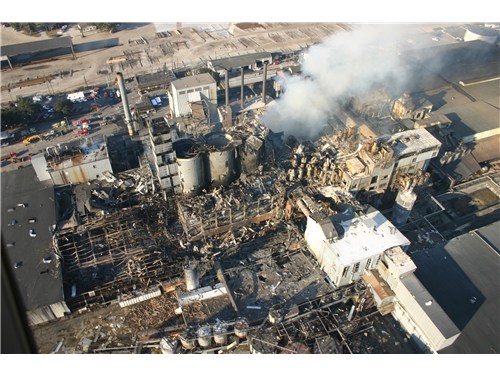
In this episode of the Dust Safety Science Podcast, we review the US Chemical Safety Board (CSB) report on the Imperial Sugar Explosion in Port Wentworth, Georgia on February 7, 2008.
The explosion and fire resulted in 14 fatalities and 38 injuries, at the Port Wentworth plant.
In the podcast episode we cover the regulatory landscape in 2008, the events that lead up to the combustible sugar dust incident, deficiencies reported by the US Chemical Safety Board and the main findings from their investigation.
The episode concludes with key take-aways from the investigation and comparing to what we have seen with the Combustible Dust Incident Database to date.
Regulatory Landscape
The February 7 2008, Imperial Sugar, Port Wentworth Refinery, (Savannah Foods), explosion occurred at a time when dust explosions where just beginning to come under the microscope in the United States.
Two years prior in 2006, the US Chemical Safety Board released its Combustible Dust Hazard Study which summarized 281 major combustible dust incidents between 1980 and 2005. In this report, the CSB recommended that the Occupational Safety and Health Administration (OSHA) issue a comprehensive combustible dust standard for general powder handling industries.
Just months after the Imperial Sugar explosion, in Port Wentworth refinery, Georgia, OSHA announced that it intended to initiate rule making towards a comprehensive combustible dust standard. In its investigation into the Imperial Sugar Explosion released in September 2009, the CSB strongly reiterated its recommendation to OSHA.
Unfortunately, at the time of writing (November, 2018), little progress has been made towards a comprehensive combustible dust standard in the United States, from OSHA.
Imperial Sugar Refining Explosion Incident
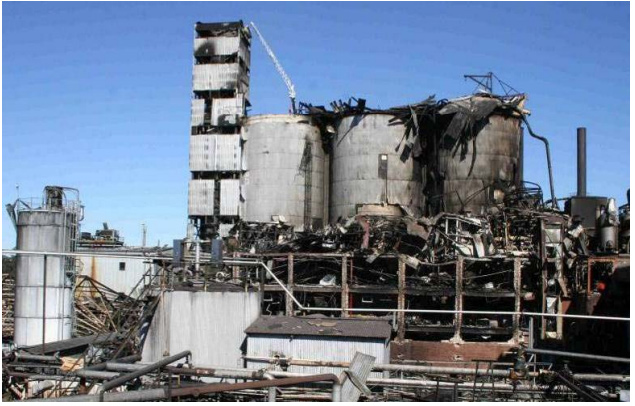
The Imperial Sugar Port Wentworth Refinery in Georgia, (Savannah foods),
consisted of a large processing facility which refined sugar. The processing facility was connected to three storage silos and the packaging and specialty products area by a large system of bucket elevators, screw conveyors, conveyor belts, and horizontal conveying systems. A massive explosion occurred in the center of the Imperial Port Wentworth site, packaging building, destroying or extensively damaging all three sugar silos and the packaging buildings that surrounded the silos.
Major Deficiencies
The Chemical Safety Board report highlights several deficiencies that contributed to the explosion incident. Two of these had a very large impact on the severity of the explosion. The first was that the conveying systems, dust collectors, and bagging systems continuously spilled sugar throughout the facility. Up to two months prior to the incident, internal documentation indicated that tons of sugar dust were routinely removed from the facility.
The second major deficiency was clogging in the conveying system below the storage silos which caused dust to spill off of the conveyor in the tunnel. Making this situation even more dangerous, a few months prior to the incident this conveyor was enclosed allowing the dust concentration to increase above the minimum explosible concentration.
Primary Explosion Ignition Sources
The US Chemical Safety Board investigation reviewed four potential ignition sources and ignition energy, for the Imperial Sugar Explosion.
- Open Flame: Ignition by open flame was ruled out as no workers were present inside the tunnel system
- Faulty Switches: Switches inside the enclosed conveyor were ruled out as the two remaining after the explosion appeared to be rated as explosion proof
- Friction Sparks: Sparks from a jammed conveyor could not be ruled out, but additional testing by the CSB demonstrated that these sparks were unlikely to ignite the sugar dust
- Hot Surface Ignition: The CSB report indicates that ignition from an overheated bearing may be the most likely ignition scenario. The conveyor was designed such that the bearings were inside the enclosure and in direct contact with the potential dust which had a Minimum Ignition Temperature ranging from 306-420 degrees Celsius.
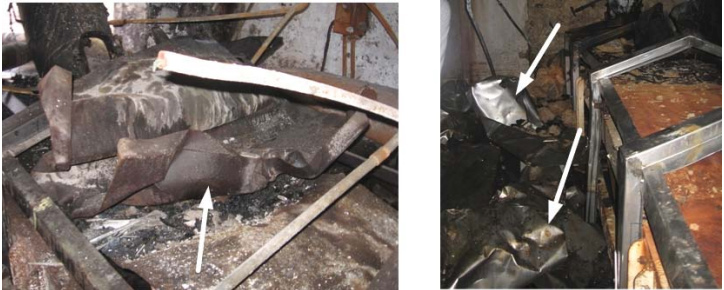
Secondary Explosions and Fires
Reports from workers and the company CEO who was walking the floor at the time of the incident, state that the initial explosion heaved the three inch concrete floors and shook the building.
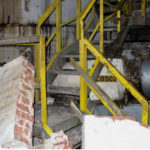
This caused the fugitive dust in the packaging building to be dislodged and dispersed allowing for subsequent explosions and fires.
Video from an adjacent business shows explosions occurring up to 15 minutes after the primary incident and fires starting up to 100 feet away from the silos.
The US Chemical Safety Board concluded that the secondary explosions and fires played an important role in the overall severity of the incident. In addition to injuring employees, these acted to knock out the power system and majority of the sprinkler systems. Knocked down walls and destroyed stairwells also played an important role in making it difficult for employees to escape the secondary fires.
Findings from the Chemical Safety Board Report
In their report, the US Chemical Safety board summarizes nine key findings, of the explosion and fire. This information is summarized here to help push these lessons forward and keep them top of mind. Please review the full incident report for the reasoning behind these findings and recommendations from their work.
1. Imperial and the granulated sugar refining, the sugar industry, and packaging industry have been aware of sugar dust explosion hazards as far back as 1925.
2. Port Wentworth facility management personnel were aware of sugar dust explosion hazards and emphasized the importance of properly designed dust handling equipment and good housekeeping practices to minimize dust accumulation as long ago as 1958, but did not take action to minimize and control dust accumulation, and the sugar dust hazards .
3. Over the years, the facility experienced granulated sugar and powdered sugar fires caused by overheated bearings or electrical devices in the packing building. However, none of these incidents resulted in a devastating dust explosion or major fire before the February 2008 incident.
4. Company management and the managers and workers at both the Port Wentworth, Georgia, and Gramercy, Louisiana, refineries did not recognize the significant hazard posed by sugar dust, despite the continuing history of near-misses.
5. The enclosure installed on the steel conveyor belt under sugar silos 1 and 2 created a confined, unventilated space where sugar dust could easily accumulate above the minimum explosible concentration.
6. The enclosed steel conveyor belt was not equipped with explosion vents to safely vent a combustible dust explosion outside the building.
7. Company management and supervisory personnel had reviewed and distributed the Occupational Safety and Health Administration Combustible Dust National Emphasis Program shortly after it was issued in October 2007, but did not promptly act to remove all significant accumulations of sugar and sugar dust throughout the packing buildings and in the silo penthouse.
8. The secondary dust explosions, rapid spreading of the fires throughout the facility, and resulting fatalities would likely not have occurred if Imperial had enforced routine housekeeping policies and procedures to remove sugar dust from overhead and elevated work surfaces and remove the large accumulations of spilled sugar throughout the packing buildings.
9. The Port Wentworth, Georgia facility risk assessment performed by insurance companies in May 2007 and the report submitted to Imperial management did not adequately address combustible dust hazards, per OSHA hazards.
Key Take-Aways
Comparing the data we have gathered from the Combustible Dust Incident Database to the incident report from the refinery explosion in Port Wentworth, Georgia, several key take-aways were outlined in concluding the podcast episode.
#1 – Risk Perception
The first take-away is the inherent difficulty in risk perception of workers and management in so-called “low-frequency” but “high-severity” catastrophic safety incidents like dust explosions. Although both management and workers were aware of the hazards of raw sugar as combustible dust and the facility had had several near-miss fires and explosions, efforts were not made to reduce the accumulation of fugitive dust in the facility which ultimately lead to the large loss of life during this incident.
#2 – Importance of Training
The second key take-away is the importance of training in preventing and responding to a process safety incidents. Lack of site specific combustible dust training, review and understanding of evacuation procedures, and lack of an effective management of change program all acted to increase the severity of the refinery explosion and fire.
#3 – Role of External Groups During Audits
The third and final take-away outlined at the end of the podcast demonstrates a potential way forward to help reduce these types of incidents in the future. Both insurance companies and industry trade association groups are reported to have audited the refinery, prior to the explosion. Although inspectors from these groups had training in recognizing combustible dust hazards, this information was not passed on to the safety and health management at the facility during these audits.
Education and encouragement of safety and health communication between these groups provides a potential avenue for stopping these type of explosions before they happen in the future.
Resources Mentioned
The resources mentioned in this episode are listed below:
US Chemical Safety Board Investigation Report:
Investigation Report – Sugar Dust Explosion and Fire
US Chemical Safety Board Video:
Inferno: Dust Explosion and Fire at Imperial Sugar
OHSA Occupational Safety and Health Administration Combustible Dust National Emphasis Program: Combustible Dust National Emphasis Program (Reissued) CPL 03-00-008
Thanks for Listening!
To share your thoughts:
- Leave a note in the comment section below
- Ask a question to be answered on the show
- Share this episode on LinkedIn, Twitter or Facebook
To help out the show:
- Subscribe to the podcast on iTunes
- Leave a review and rate our show in iTunes to help the podcast reach more people
Download the Episode
Full Episode Transcript
Chris Cloney: [00:09] Welcome to episode number three of the Dust Safety Science Podcast, where we’re looking at increasing awareness of combustible dust hazards, generating lessons learned from fire and explosion incidents, and creating a connected global community around dust safety in powder handling industries. In today’s episode, we’ll be reviewing the Imperial Sugar Refinery explosion on February 7th, 2008. In this episode, we’ll be going through the US Chemical Safety Board investigation report and pulling out the lessons learned that they found from this incident. In today’s episode, we’ll be looking at the regulatory landscape at the time of the incident, go through in detail what actually happened and the explosions ensuing fires. Look at the key findings from the CSB report, and look at three important takeaways in comparison with what we’ve learned from the Combustibles Incident database. As always, you can go to the show notes for this episode by going to dustsafetyscience.com/the episode number. So in this case it’d be dustsafetyscience.com/3. And if you enjoy it, I have been enjoying the podcast so far. Go ahead and rate and review us in iTunes. If you have any questions, feel free to go to dustsafetyscience.com/ask. And you can ask those questions there either verbally or or write by writing them down. And we’ll have them answer here on the show. We’ll bring on experts to talk about those questions. We’ll go into the research archives and find that material. So with that, I want to say thank you again for listening and I hope you enjoy the show.
Chris: [01:36] Today’s episode will be a solo show focusing on the Imperial Sugar Refinery explosion in Wentworth, Georgia. That’s just outside Savannah. February 7th, 2008. So this incident had a very large impact on the combustible dust community. It was quite a severe incident. There were over 14 fatalities, 36 injuries. And it came at a time when the awareness of combustible dust hazards was increasing. The National Emphasis Program had just been released by OSHA two months prior to this incident occurring. And then after this incident before the CSB, the Chemical Safety Board report came out. Osha renewed its stance that it would move forward with rulemaking towards federal combustible dust standards. So then the purpose of this episode really has a couple parts to it. One is to carry forward the lessons learned generated from the US Chemical Safety Board and the 90 page report they released over a year after the incident, where they actually sent a team out for four months to analyze the the destruction after the explosion and look at documents from the company do interviews with witnesses and really pulled together a lot of great information that we can then learn from moving forward with combustible dust safety. Also, it’s a good way to keep the discussion going if you’re a process safety professional. Work at installation of explosion or fire safety equipment, or even manufacturing this equipment, it’s good to generate the information or lessons learned around these incidents.
Chris: [03:04] And in particular, I’ll go over a couple key takeaways. From reading the report on my side, I’ll also cover the CSB recommendations in this podcast. So that really is helpful for people that are involved in the safety side and have a good background knowledge already if you’re a safety manager or a sales person, selling, say, original manufactured equipment, it’s also helpful to have a background understanding of how large scale incidents like this happen. And then when you go and talk to your customers or your workers at your facility, you have a larger knowledge base from which you can draw on to illustrate the hazards that are involved. If you have any thoughts or questions about this specific episode or the Imperial Sugar Refinery incident, or even some comments on how it affected you and your professional progression, you can go to the website Dust Safety science.com/episode three and leave a comment there. At the time of the incident, Imperial Sugar Refinery was one of the largest sugar refineries in the US, taking in raw cane sugar and processing into refined sugars, including granulated sugar and other specialty products. The explosion itself completely destroyed the large three storage silos that were on site, as well as the full packing facility. So the facility layout had a processing operation in which the refined sugar was then transported using screw conveyors, bucket elevators, and horizontal conveyors into the three storage silos.
Chris: [04:27] Underneath the storage silos was a tunnel system that was seven feet tall and 12ft wide, and had an 80 foot conveyor horizontal conveyor that went underneath each of the silos. So the furniture came in. Silo number three fell down onto an arrow belt conveyor into the bucket pit, and then was picked up by bucket elevators into silo number two and silo number one. These dropped out into a steel horizontal conveyor system, which then took them into the screw conveyors and bucket elevators that took the refined sugar into the packaging facility, as well as into the specialty products facilities where they made their products, such as brown sugar and liquid sugar. The US Chemical Safety Board report highlights several deficiencies in the processing operations, in the packaging plants and in the tunnel underneath the silo system. Two of these had a very large impact on the overall severity of the explosion. The first thing was that in the packing facility, the screw conveyors, the bucket elevators were not dust tight. So there’s a lot of dust leakage. As well as that, the bagging stations and filling stations, there’s a lot of dust being spilled out even up to two months prior to the incident. There is documentation from the company reporting over several tons of sugar dust being removed routinely from the processing floor.
Chris: [05:48] From these dust accumulations in a combination with this, they had an ineffective dust collection system. Several of the dust collectors were undersized as well as some of them were not in operable operating conditions. Afterwards, the CSB looked at several of the pipes and ductwork and found they were completely clogged with sugar dust. Sugar dust was not moving. This deficiency meant that at any point, if a flash fire and explosion did occur, there’s a very large chance, a very large probability of having a secondary explosion and several secondary fires that could be quite severe. And that’s actually what happened in this case. The second major deficiency that led to the actual ignition and primary explosion in this case was in the tunnel system underneath the storage silos. So routinely they would have blockages and clogs in the bottom of the silo, which would then cause the oncoming sugar dust that was on the conveyor system to fall off the sides, or jam up or get dispersed into the air in the tunnel system. This is actually occurring for over 80 years of the facility. They have documentation going back that far showing these sorts of issues, both in the packaging facility with dust, all dust accumulations on the floor, on the rafters, but also in this tunnel system, because the tunnel is so large, it was seven feet by 12 ft. You never got up above the minimum explosive concentration of the dust.
Chris: [07:11] All of that changed a few months prior to the incident, when they enclosed the horizontal conveying system underneath the storage silos. They did this for sanitary reasons. They didn’t want material falling out into the sugar as it goes into the packing plant. So they enclose the conveyor system. In this they also enclose the switches. They enclose the bearings all inside a steel frame with steel plating or metal plating going down the side of the 80 foot conveyor. So now in the facility we have the conditions to have a primary explosion occur in the tunnel system underneath the silos, but also for this to propagate up through the bucket elevators, up through the screw conveyors into the packaging facility, which then has this housekeeping issue which can then lead to large secondary explosions and fires. And that’s indeed what happened February 7th at about 7:15 p.m.. At this time, the new CEO of Imperial Sugar Company was actually touring the facility. He had just been made CEO nine days prior. Which just goes to show that these incidents can happen at any time, even when a safety professional or the CEO or someone else is walking the facility. The group reported that they were startled when they heard a loud noise coming from the packaging facility. That sounded like a large pallet of packaging material falling off a forklift. 3 to 5 seconds later, they heard a loud explosion which actually knocked them to the floor.
Chris: [008:36] Heaved the concrete floors, which were three inches thick and knocked out several walls. This was followed by a series of secondary explosions and fires that occurred up to 100 ft away from the storage silo system throughout the entire packing facility. Video footage from a nearby business shows how terrifying and devastating the extent of the damage is, and saw a large fireball shooting the air up to 15 minutes after the initial primary explosion incident. From interviewing witnesses and looking at the the explosion damage within the facility, the Chemical Safety Board concluded that the explosion was initiated beneath the silo number one, and that it occurred due to a clog or a lump that gets stuck in the bottom of the silo chute, which then caused overflow of sugar from silo number two as it moved along the steel belt. This filled the new enclosed conveying system, allowing the dust concentration to get above the MEC. They looked at several possible ignition sources. They ruled out open flame as there were no workers in the silo system itself. There were four electrical switches inside the enclosure. Two of those remained after the explosion. Both had explosion safety ratings. So they ruled those out. They couldn’t rule out metal to metal friction sparks from, say, a jammed conveyor. But they did do testing. They were unable to ignite the dust.
Chris: [10:04] With testing after the incident, they conclude that overheated bearings most likely caused the initial explosion event in the conveyor system, so the bearings overheated, getting above the mitt of the sugar dust, which was around 400°C or 700°F. An interesting aspect that we have in this particular incident is that the CSB actually went through and looked at how this primary explosion ended up propagating through with the rest of the facility, which we normally are typically not in every sort of incident. This took a team again over four months to conduct the analysis. So what they believe happened was this initial explosion in the conveyor system. It propagated throughout the entire conveyor, all 80ft, every metal panel that was on the side of the structure they put on was blown off quite violently. So they were twisted. They were torn. The pressure wave went between silo two and silo one, and knocked out the brick wall that was housing the stairwell adjacent to the silos, and also heaved the three inch concrete floors above. This dislodged a lot of dust from the rafters, from the floors that accumulated around the area. And this led to the secondary explosions and fires, again, up to 100 ft away from the initial ignition location. Another difficulty with the resulting secondary explosions, where they knocked out the power system within the facility and also knocked out all the sprinkler systems or most of the sprinkler systems.
Chris: [11:38] So now the sprinklers couldn’t activate to put out the fires, and workers couldn’t see where they were going. After the incident the analysis by CSB showed that there was limited training. They did have exit guidelines from different locations, but they weren’t specific to where different workers were within the facility. And they certainly didn’t take into account the fact that walls may be knocked down and that stairwells may be inoperable. Beyond that, the CSB couldn’t find any records of fire drills or escape drills that took into account any sort of explosion or, or scenario similar to the fires that they saw here. Before jumping into some of the takeaways that I have from reading the report and comparing to what we found with the Combustible Dust Incident database, I just want to give a summary of the Chemical Safety Board findings just because they highlight a lot of the issues that occurred. The first finding was that the Imperial Sugar Company and the larger sugar handling industry as a whole, has had awareness of combustibles hazards since 1952. CSB found that the facility management since 1958 has documented precautionary measures and equipment design in relation to reducing the chance of an explosion from occurring and the severity. However, they did not take action to minimize or control the sugar dust hazards that were found in the packing area.
Chris: [13:06] And below in the silos and the tunnel system. Over the years, the facility had experienced several small, smaller scale explosions. And many fires in different equipment. And at no point did that ever escalate to the severity that we saw on February 7th, even though that plan had been operating in that way for over 80 years. The Chemical Safety Board found that the enclosure of the horizontal conveyors under the silo systems was. The large was the contributing factor to initiating the explosion event. And also found that the conveying system did not have any sort of venting to reduce the effect of the explosion once it had initiated. Because the explosion was unmitigated. This allowed the pressure rise to to build up to destructive levels, both in the conveyor blowing off the panels, but also through the side walls and roof, dislodging the concrete slabs which further disperse more dust in the air and cause the secondary explosions. The CSB found that the fatalities and injuries most likely occurred during the secondary explosions and resulting fires, and due to difficulties in employees actually evacuating the building once the incident occurred in the last two. Key findings the CSB found that the company management and supervisory personnel had reviewed and distributed the OSHA National Emphasis Program a few months prior to the incident. However, they did not act promptly to remove the significant accumulations of sugar dust found through the packing facility or take into account the difficulties that they may have in the tunnel system underneath the silos.
Chris: [14:46] In the last set of key findings, the Chemical Safety Board found that risk insurers that did audits in 2007, as well as trade associations that did audits. In May of 2007. Gave ratings to the facility that were indicative that they did not have a significant hazard involved. However, both of these trade associations and the risk insurers or the property insurers knew about the hazards of combustible dust, however, did not relay that information through to the facility in a way that caused them to to reduce the chances, the likelihood or severity of a resulting explosion. So I want to conclude this podcast episode by talking about some key takeaways from the CSB report and from this incident in general that aren’t necessarily covered in the report, but that we’ve seen in relation to the Combustible Dust Incident Database. I want to give three key takeaways. The first is about understanding the nature of the problem that we’re dealing with and risk perception of that kind of combustible dust hazard. The second is the role that training needs to play in prevention of explosion incidents and response to the incidents. And third, I want to talk a bit about some lessons that this specific incident has and the CSB report has on how potential ways that we can change this moving forward. The first major takeaway is to do with, again, with this risk perception in this uphill battle that we really do have in combustible dust incidence because these are low frequency and, and sometimes high severity, as in this case, incidents.
Chris: [16:23] In my work, I often talk about different levels of understanding of combustibles hazards. So the first level is just awareness that that combustible dust can pose a fire and explosion hazard. The second level is knowledge. So we know that a hazard exists. But how bad can that be? In a lot of cases in a lot of facilities, we underestimate the potential consequence. Third level is connection. So, okay, we know there’s a hazard, how bad it can be, but who do we go to to get the right information? To get the right equipment put in place. And then the fourth level is risk perception. So because these are low frequency events, we often become normalized or complacent to the potential consequence of an explosion event. You often hear this as I’ve been here 20 years and that’s never been an issue. This facility has been operating this way for 80 years, for 100 years, and we’ve never had any. So then the first takeaway is really that this plant had been operating under these conditions of a lot of fugitive sugar dust in the packing facility. A lot of dust was spilled in the tunnel for over 80 years before they had this catastrophic incident, and it wasn’t due to lack of ignition sources.
Chris: [17:32] This modification to the tunnel system wasn’t the only primary explosion to occur. The earliest explosion that was documented at the facility was in 1961, in the powdered sugar mill, which again is adjacent to the packaging factory or packaging facility. They had frequently reported fires throughout the facility as dust accumulations grew on top of motors and overheated them, and even two months prior to the February 7th incident, they had an explosion in a dust collector unit near the roof, which was successfully vented and didn’t act to initiate a secondary explosion. This just shows that very frequently they were having explosions, having fires, and even occasionally having explosions that all could have served as an initiating event for this large scale explosion. This highlights the difficulty that we are going to have as a powder safety community, as a dust processing community in illustrating increasing awareness and knowledge around these hazards. This isn’t to be discouraging, but it’s just to highlight that this is the nature of the problem that we’re trying to solve. The second key takeaway is the role that training had in this incident, and it actually impacted in a couple of different ways. The CSB went over 10,000 pages worth of safety training at the Imperial Sugar Refinery in Port Wentworth, and found very good mention of specific safety rules for that plant facility, but no coverage of combustible dust.
Chris: [19:02] At least over the last decade of of training, there’s also no training done on evacuation in the sense that they didn’t do practice drills or what if scenarios, even though they had so much fuel accumulated and the possibility of an explosion or a fire may be seen as quite large. The last area we’re training really comes involved in this is in this concept of management of change. And we’ll cover this in a later podcast episode, quite in more detail and maybe bring some experts on to discuss it. But the whole process of enclosing the tunnel system, the conveyor in the tunnel is a pretty big change. The processing operation. And if they had done a proper management change analysis, they may have picked up on the potential consequence that would have of getting the dust above the minimum explosive concentration and triggering the specific explosion event on February 7th. So these first two takeaways may be seen as a little bit discouraging, just showing the difficulties we have in both preparing for and mitigating the explosion event as it occurs. The third takeaway is based on some recommendations in the CSB report and actually shows a way forward. So the CSB found that the property insurers had done an audit in 2007 at the facility in May 2007, and that a trade association that they belonged to had also done an audit of the facility.
Chris: [20:28] The property insurers did not mention any difficulty with combustible dust, and the trade association gave them a supreme rating, but it was only based on the cleanliness and based on the quality of the foodstuffs being produced. It didn’t have anything to do with explosion or fire safety. However, both these associations, when interviewed after, showed that they did have training material for their inspectors around combustible dust and that the inspectors did know of these hazards, but they didn’t pass that information along to the Imperial Sugar Refinery and didn’t pick up on it while they were. They were going through the facility. So this this gives us a way forward in that these trade associations and the property insurers really can play a role in educating the plan owners and the facility owners that these are issues, maybe push them towards a material that would better highlight the potential consequence and give them a place to go to mitigate and prevent these sort of explosions from happening further. And with that, I want to thank you again for listening to the Dust Safety Science podcast. If you’d like to get access to the US Chemical Safety Board investigation reports or the videos that they create on this incident. You can go to dustsafetyscience.com/3. If you have a question that you’d like to ask the Dust Safety Community, have an answer on the podcast. You can go to dustsafetyscience.com/ask. Get that question answered there.