Updated September 24, 2024 Authored by Dr. Chris Cloney and Jon Barrett of Dust Safety Science
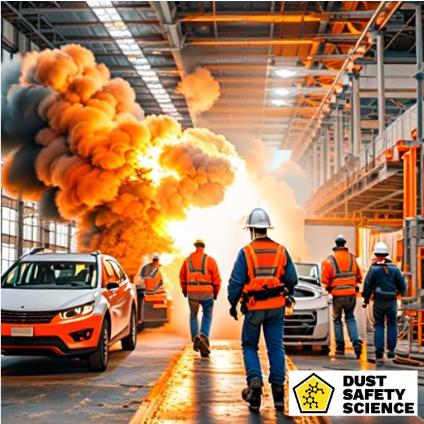
Key Takeaways:
- Industry Dynamics: The automotive industry, a vital pillar of modern manufacturing, faces a significant but often overlooked hazard, combustible dust. Understanding the correlation between automotive processes and the generation of combustible dust is essential for maintaining safety standards.
- Hazards of Various Materials: Automotive manufacturing involves an array of materials like metals (aluminum, magnesium, steel, titanium) and organic substances (plastics, resins, rubber). Machining, welding, finishing, and molding operations generate fine dust particles from these materials, which, when suspended in the air, land above suspended ceilings, elevating the risk of fire or dust explosions.
- Industry-Specific Concerns: Specific equipment used in automotive manufacturing, including CNC machines, grinders, sanders, and welding stations, contributes to the creation and dispersion of combustible dust, which requires specialized dust collectors and dust collection.
The Automotive Industry and Potential Risks
The automotive industry including General Motors, Ford, and Tesla, stands as a cornerstone of modern manufacturing, driving innovation, mobility, and economic growth globally. Amidst the whirring machinery and meticulous auto production, an often underestimated hazard lurks, combustible dust. Aluminum dust, magnesium dust, and titanium dust can cause dust explosions. Understanding the correlation between automotive manufacturing and combustible dust is pivotal for maintaining workplace safety standards and mitigating a possible dust explosion within this thriving auto supplier industry.
Introduction to the Combustible Dust Hazards
In the auto industry, the generation of combustible dust stems from various materials and processes employed in manufacturing. The Occupational Safety and Health Administration, (OSHA), identifies Metal as a Combustible Dust. Fine particles generated during various stages of metal fabrication, such as cutting, grinding, and polishing constitute the primary source of combustible dust in these facilities. Metals like aluminum, magnesium, steel, titanium, and hexavalent chromium, extensively used in vehicle components, are prone to producing fine dust particles during machining, grinding, welding, and finishing operations. Aluminum dust, when dispersed in the air, as a dust cloud, can catch fire, and pose a significant hazard due to its combustible properties. The highly reactive nature of these metal particles, particularly steel dust and magnesium dust, presents an increased risk of ignition when exposed to certain conditions such as static electricity, or gaseous fire fuels like carbon dioxide, creating such intense air pressure that it creates an explosion.
Beyond metals, other materials utilized in an auto supplier and in automotive manufacturing plant, such as plastics, resins, and rubber, also create an additional maintenance project and contribute to the combustible dusts hazard. Using a hand grinder, cutting, molding, or sanding processes, these materials generate finely divided solid particles. When metals are also subjected to machining, grinding with a hand grinder, or welding processes in an auto supplier, it creates an ignition source such as sparks, and creates a dust and a fire hazard. These processes produce fine dust particles, such as zirconium dust and hexavalent chromium, that pose inherent risks for a primary or secondary dust explosion. These actions require specialized dust collectors, dust collection equipment, and filtration equipment to prevent an explosion hazard.
The Automotive Industry Specific Concerns with Dust Explosions
The auto industry presents unique equipment and operational concerns regarding combustible dust. Machinery like CNC (Computer Numerical Control) machines, grinders, sanders, and welding stations used in an auto supplier and auto manufacturing generate significant steel dust and other particles from metals and other materials. The high-speed operations involved in a hand grinder, contribute to the creation of fine steel dust and other metal dusts, that can linger in the air or settle within the dust collection equipment, ventilation systems, enclosed space, or confined space in other workspaces, and require additional health administration assistance with emergencies. Ignition sources such as sparks from a hand grinder can set off a fire hazard with extreme heat, and a primary dust explosion. As a result of the initial sparks from a hand grinder, a secondary explosion is also possible.
Moreover, the presence of flammable liquids, solvents, or coatings used in automotive painting or finishing operations introduces additional hazards, for a potential explosion. The Detroit Free Press has provided dust incidents, as a news release relating to dust hazards where an explosion caused major damage in the auto manufacturing region. Major auto manufacturers such as General Motors, and automotive supplier Ford are in this region. Attached are some Detroit Free Press dust explosions, as a news release. According to the Detroit Free Press, an example of a dust explosion news release occurred at an Aluminum Alloy Wheel Manufacturer. In addition, another news release, from the Detroit Free Press also reported a blast furnace explosion that injured 15 workers at U.S. Steel’s Great Lakes Works plant on Zug Island. OSHA published a similar news release, with an auto supplier dust collector explosion.
Electric Vehicle Batteries and the Dangers with Combustible Dust
General Motors, Ford, Tesla, auto supplier BYD, and other auto manufacturing companies, have increased production with electric vehicles. Electric vehicle (EV) batteries have become integral components in the auto industry, promising environmentally friendly transportation alternatives. However, the production and handling of these batteries within an automotive supplier, risks potential health problems and hazards, especially concerning dusts, as outlined by the NFPA 484 Standard for Combustible Metals.
EV batteries primarily consist of lithium-ion cells, which contain highly reactive materials. During manufacturing like electrode coating, electrolyte filling, and cell assembly, there is a possibility of generating fine particulate matter or dust. A recent news release, Firefighters Respond to a Heating System Fire at a German E-Vehicle Company, states fires occasionally occur with EV batteries.
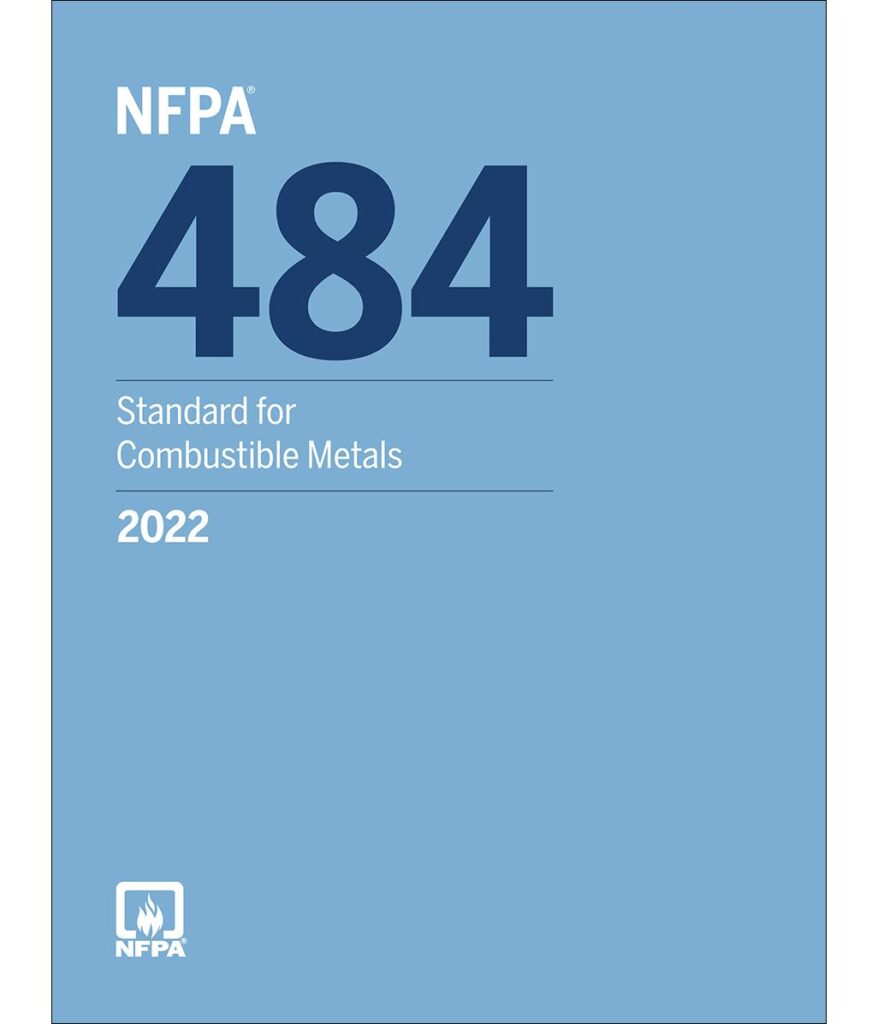
NFPA 484 Standard for Combustible Metals
This National Fire Protection Association standard 484, applies to the production, processing, finishing, handling, recycling, storage, and use of all metals and alloys that are in a form that is capable of combustion or explosion, as well as to operations where metal or metal alloys are subjected to processing or finishing operations that produce combustible powder or dust. For instance, ignition sources such as sparks from a hand grinder could ignite aluminum, chip processing could ignite aluminum, or polishing aluminum wheels creates sparks, and creates dust, possibly igniting a dust cloud and a dust explosion.
The NFPA 484 standard for combustible metals (2022), originally designed for metals and alloys, applies to various operations involving metals such as metal lithium dust, that can undergo combustion or explosion, including those operations where metal fabrication generates combustible powder or dust. While EV batteries may not inherently consist of combustible material, the lithium-ion chemistry utilized in these batteries can produce combustible dust if mishandled during production, recycling, or disposal.
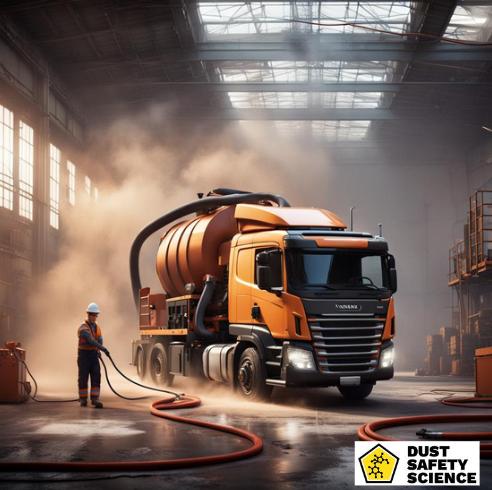
EV Battery Production and Handling, Provides many Hazards and Risks:
An automotive supplier with Electric vehicle (EV) battery production and handling poses numerous hazards, potential health problems, and risks, with combustible dusts being a significant concern. The manufacturing processes involved in EV battery production, such as electrode coating, electrolyte filling, and cell assembly, can generate fine particulate matter containing highly reactive materials like lithium compounds. When dispersed in the air, this dust can become combustible, leading to explosion hazards.
While specific standards and codes may not directly address EV battery production, the NFPA 484 Standard for Combustible Metals offers guidelines for managing combustible dusts in metal processing operations, such as sparks with a hand grinder, and dust collection, which can be applied to mitigate risks in battery manufacturing facilities.
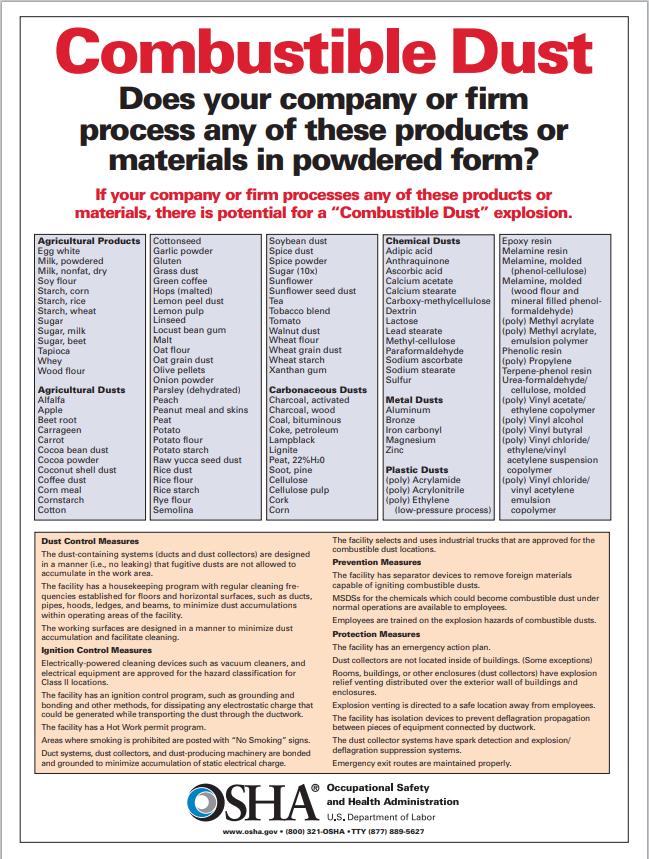
Conclusion
As the automotive industry with companies like General Motors, Ford, Tesla, and BYD, continues to evolve with the widespread adoption of electric vehicles (EVs), it faces new challenges concerning combustible dusts. While traditional auto manufacturing has long been accustomed to producing metal dust hazards, such as sparks with a hand grinder, the emergence of EV batteries introduces a new maintenance project, to further prevent dust hazards. Electric vehicle (EV) battery production presents a transformative shift toward sustainable transportation, but it also introduces new hazards, notably combustible dust. While specific standards and codes may not directly address EV battery production, guidelines such as the NFPA 484 Standard for Combustible Metals offer valuable insights for managing combustible dust hazards, for every safety engineer, within an automotive supplier.
About Dust Safety Science
For more from Dr. Chris Cloney on Combustible Dust in Waste and EV Factories, visit this podcast episode: Fire Hazards in Waste and Recycling Facilities with Ryan Fogelman
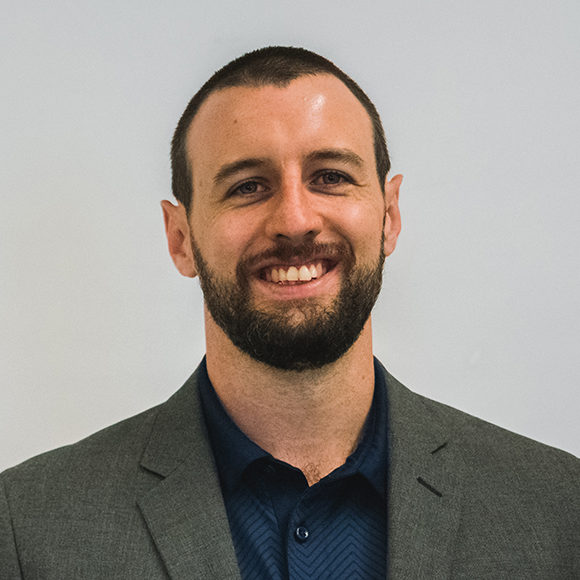
Resources:
Visit Dust Safety Science (Global Incident Tracking)
Visit Dust Safety Academy (Resources, Training and Events)
Visit Dust Safety Professionals (Need Help? Get Support Today!)
Visit Dust Safety Journal for the Dust Safety Science Monthly Journal
Subscribe to our Dust Safety Science Newsletter at Dust Safety Science Newsletter
Visit the Dust Safety Science blog for written articles on combustible dust safety including the latest research, expert opinions, and state-of-the art in fire and explosion protection.